LPP Logistics develops proprietary Control Tower platform for global supply chain management
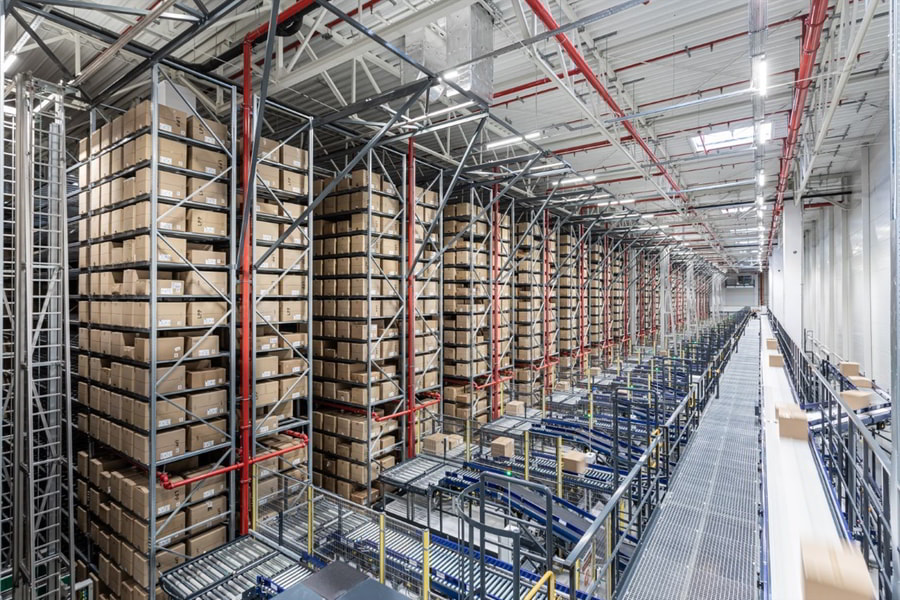
In response to the challenges of managing an international supply and distribution network, LPP Logistics has implemented a proprietary Control Tower platform project. The system, developed by the experts of LPP Logistics – a company belonging to the LPP Group – allows to control the flow of goods at particular stages of the import supply chain, streamlines electronic document circulation and provides real-time information to all its participants: from buyers to suppliers, distribution centres, and shipping agents. It also renders it possible to optimise logistics processes in terms of costs and operations and to react quickly to changing market conditions. The platform received a distinction for the best project in the 15th edition of the Polish Logistics Association Awards.
The global supply and distribution chain of the Polish clothing company, managed by LPP Logistics, covers nearly 40 sales markets and 18 manufacturing countries in Europe and Asia. The large dispersion of the supply chain and the time differences separating its individual links posed a challenge for the company in terms of efficient communication. Given the need to synchronise logistics operations on such a large scale and monitor them on an ongoing basis, the company decided to implement its own tool to centrally manage the electronic information flow in real time. The Control Tower system implemented by the company allows the continuous execution of complex operations, control of the flow of goods and communication with all participants in the supply chain. These include buyers, over 1,200 international suppliers, two distribution centres, a team responsible for managing the logistics area in Poland and Asia, as well as shipping agents operating in Asian markets.
– The past years have been dominated by turbulence in supply chains. This has forced on business to adapt quickly and efficiently to external market conditions. Our response to the dynamically changing environment was to implement a bespoke Control Tower platform for LPP Logistics. Therefore, we are able to detect – in real time – any deviations in the very process of goods flow between individual links in the chain. We are also able to correct any irregularities that arise, from the peripheral processes carried out by the factory, through transport booking for finished shipments, documentation, to the process of delivering the final product to our distribution centres – comments Małgorzata Bogdziewicz, Supply Chain Management Director, LPP Logistics.
One of the first modules of the Control Tower platform to be implemented was the Supplier Portal where suppliers from all production countries generate logistics labels themselves, which allows them to standardise packaging and optimise the use of warehouse space. In addition, they prepare and send shipping documents for inspection, and declare the readiness of manufactured goods for transport, while declaring the contents of the shipment and booking transport time and space with the carrier. Control Tower also ensures supervision of the handover of goods to the transport company and consolidation of cargo. Also, full registration of deliveries in transport is performed – from the moment of shipment to the final receipt of goods into the warehouse. The platform is integrated with the WMS systems of LPP Logistics’ distribution centres and the customs system, in which the company’s customs agents perform clearance for all types of imported LPP Group deliveries. Works are currently underway on the implementation of further functionalities enabling the management of containers’ transportation from the port or adapting Control Tower to the needs of LPP Logistics as a logistics operator for customers outside LPP Group.
– The platform significantly improves the efficiency of planning and adjusting logistics processes to the actual deadlines on the production or transport end. Having full monitoring and control of each stage, we are able to make the most optimal use of, among others, transport or warehouse space for our goods. We are already noticing the effects of this, as following the launch of the Supplier Portal module alone, the utilisation of the automated warehouse in our distribution centre in Pruszcz Gdański has increased by as much as 20%, i.e. by 15,000 square metres. This means that without further investment, we gained additional space for 240,000 boxes – explains Małgorzata Bogdziewicz.
The complex process of developing and implementing the platform is the result of the work performed by LPP Logistics’ team of experts and Silky Coders’ team, responsible for the IT area of the LPP Group. In order to ensure the functionality and intuitiveness of the system, following a detailed analysis of the business challenges, selected suppliers were also invited to cooperate, who, together with representatives of LPP offices in Dhaka and Shanghai, were involved in the tool development process. The system, available in three language versions, enables the handling of over 85,000 orders and accompanying shipments in the global supply chain by all modes of transport.
– After a thorough analysis of the SCM (Supply Chain Management) systems available on the market, we decided to develop our own solution tailored to the fashion retail industry. A major challenge was to create a platform adapted to the scale and geographical dispersion of the LPP Group’s supply chain. An additional difficulty was related o overcoming the time and language differences of the system users, or the diverse transport methods and the very specific nature of LPP Logistics’ SCM. Control Tower was developed in a microservice architecture, which means that individual modules of the platform can be developed independently and thus supplemented with new functionalities, as well as adjusted on an ongoing basis to changing order volumes – emphasises Małgorzata Bogdziewicz.
In addition to creating new operational capabilities in handling the supply process, the implementation of Control Tower brings about measurable environmental benefits. The use of the Supplier Portal module and the implementation of a standardisation process for shipping orders from factories, in addition to specific savings in warehouse space, generated additional benefits. More efficient management of shipping containers, or a reduction in courier shipments, translates into a real reduction in CO2 emissions. The digitalisation of the information flow and partial abandonment of printed documents is also a major advantage of the platform.
– It should be noted that Control Tower is not a complete system yet. We are still developing further functionalities that will allow even better monitoring of SCM or additional improvements in the entire supply management process. Nevertheless, already at this stage, the platform is bringing us a favourable economic and environmental balance. It minimises the number of potential human errors, increases the productivity of teams and, most importantly, in an era of increasingly unpredictable business conditions, increases the likelihood of detecting possible disruptions at any stage of the logistics process. Control Tower is currently one of the key projects we are implementing, which in the future will also support our external customer service activities – concludes Małgorzata Bogdziewicz.
The LPP Group’s proprietary project has been recognised by the jury of the 15th edition of the Polish Logistics Association Awards competition, in which implementation of innovative technologies or state of the art organisational solutions improving logistics processes are recognised.
__________________________________________
LPP Logistics is a logistics operator managing LPP Group’s procurement and distribution network comprising distribution centres and Fulfillment Centres with a total area of nearly 450,000 square metres. It operates on three continents providing a full range of logistics services – from sea, rail and road freight, through the operation of its own customs agency, to advanced warehouse logistics using modern systems such as WMS, warehouse automation and Warehouse Intelligence solutions based on artificial intelligence algorithms.
LPP is a Polish family business and one of the fastest growing clothing companies in the region of Central and Eastern Europe. For 30 years, it has been successfully operating in Poland and abroad, offering its collections in such prestigious capitals as London, Helsinki or Tel Aviv. LPP SA manages five fashion brands: Reserved, Cropp, House, Mohito, and Sinsay, whose offer is available today in stationary and online stores in nearly 40 markets worldwide. The company has a chain of over 1800 stores with the total area of 1.5 million m2. LPP also plays an important role as it employs over 24 thousand people in its offices and sales structures in Poland, Europe, Asia, and Africa. The company is listed on the Warsaw Stock Exchange in the WIG20 index and belongs to the prestigious MSCI Poland index.